Finest Practices for Preventing Weld Undercut: Grasping the Fundamentals
Finest Practices for Preventing Weld Undercut: Grasping the Fundamentals
Blog Article
Mastering the Art of Welding: Exactly How to Avoid Undercut Welding Issues for Flawless Manufacture Outcomes
By understanding the origin triggers of undercut welding and implementing efficient techniques to prevent it, welders can boost their craft to new degrees of quality. In the pursuit of flawless construction outcomes, understanding the art of welding to prevent undercut problems is not simply a skill but a need for those aiming for excellence in their job.
Understanding Undercut Welding
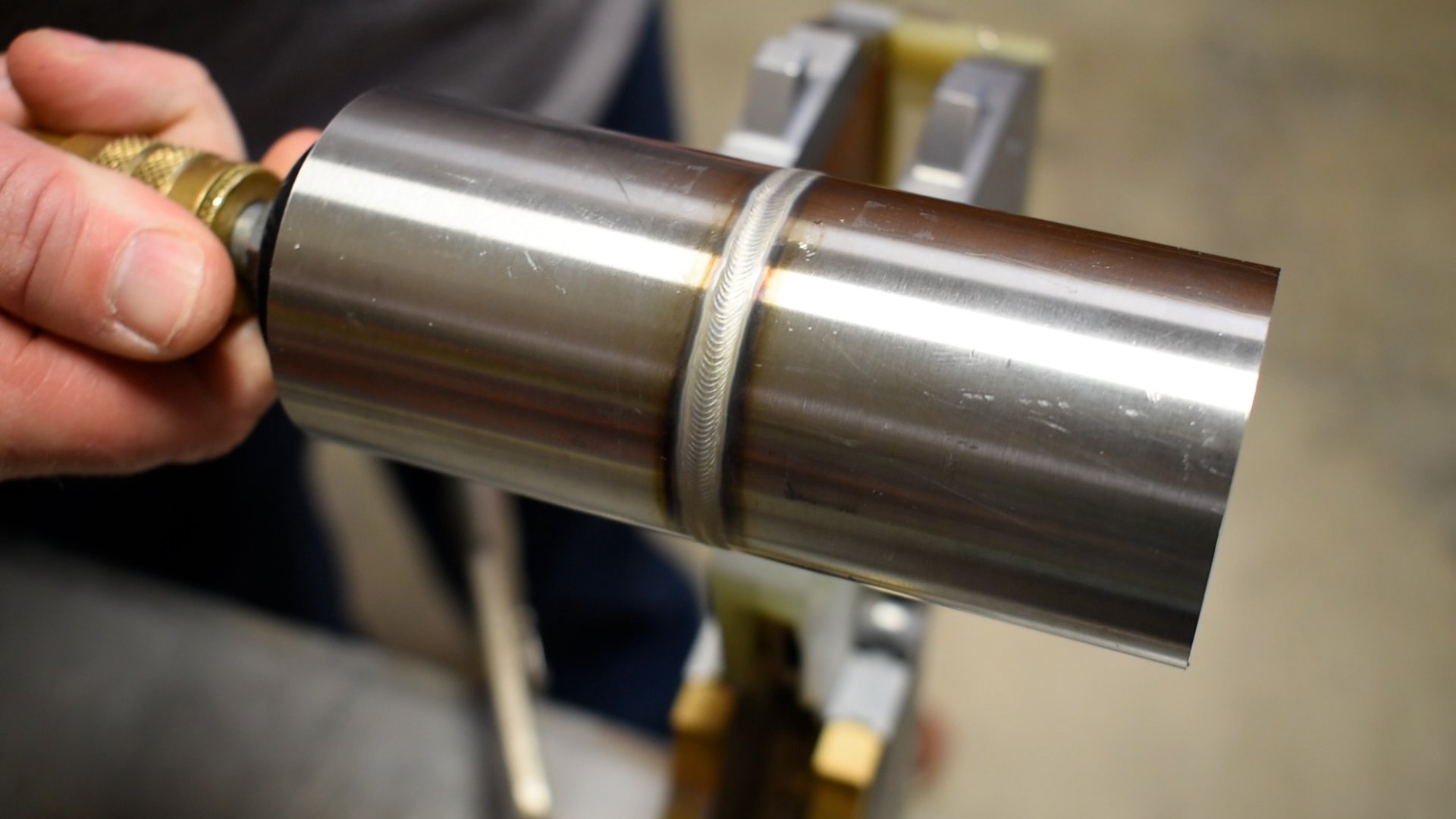
To avoid undercut welding, welders need to make certain correct welding criteria, such as changing the current, voltage, traveling speed, and keeping the appropriate electrode angle. Furthermore, utilizing the ideal welding technique for the details joint setup is vital. Utilizing weaving activities or backstepping strategies can assist make certain correct weld metal deposition and lower the probability of undercut development. Normal inspection of welds during and after the welding process is additionally critical to capture any type of undercut early and make needed modifications to stop further flaws. Preventing weld undercut. By comprehending the root causes of undercut welding and applying preventive steps, welders can achieve high-quality, structurally audio welds.
Reasons For Undercut in Welding
Understanding the elements that contribute to damage in welding is important for welders to generate top notch, structurally audio welds. Inadequate welding present or incorrect welding speed can also add to damage. Understanding these causes and carrying out proper welding methods can help protect against undercutting concerns, making sure solid and durable welds.
Techniques to avoid Undercutting

To mitigate the threat of undercutting in welding, welders can use critical welding techniques focused on enhancing the high quality and stability of the weld joints. One efficient method is to adjust the welding criteria, such as voltage, existing, and travel rate, to make certain correct warm input and deposition. Maintaining an ideal electrode angle and making sure constant travel rate can also help stop undercut. Additionally, utilizing the appropriate welding technique for the details joint setup, such as weave or stringer grains, can add to reducing damaging. Preventing weld undercut.
Utilizing back-step welding strategies and regulating the weld bead profile can also help distribute warm equally and minimize the threat of undercut. you could check here Normal inspection of the weld joint throughout and after welding, as well as implementing high quality guarantee measures, can help in discovering and addressing damaging issues quickly.
Value of Appropriate Welding Parameters
Choosing and maintaining ideal welding specifications is necessary for achieving successful welds with very little flaws. Welding criteria refer to variables such as voltage, current, travel rate, electrode angle, and securing gas flow rate that straight impact the welding procedure. These specifications have to be carefully readjusted based on the kind of product being bonded, its density, and the welding strategy used.
Correct welding specifications guarantee the correct amount of warmth is applied to thaw the base steels and filler material uniformly. If the criteria are established too expensive, it can bring about excessive warmth input, creating burn-through, spatter, or distortion. On the other hand, if the specifications are also low, insufficient fusion, absence of infiltration, or damaging might take place.
Quality Control in Welding Operations
Conclusion
To conclude, mastering the art of welding requires a thorough understanding of undercut welding, its causes, and techniques to stop it. By making sure proper welding parameters and executing quality control methods, flawless fabrication outcomes can be accomplished. It is crucial for welders to constantly pursue excellence in their welding operations to prevent undercut problems and create high-grade welds.
Undercut welding, an usual problem in welding processes, happens when the weld metal find out here now doesn't effectively load the groove and leaves a groove or anxiety along the bonded joint.To protect against undercut welding, welders must make sure proper welding parameters, such as readjusting the present, voltage, travel rate, and keeping the correct electrode angle. Inadequate welding present or wrong welding rate can likewise contribute to damage.To alleviate the danger of damaging in welding, welders can use strategic welding strategies intended at boosting the high quality and stability of the weld joints.In conclusion, grasping the art of welding needs a complete understanding of undercut welding, its reasons, and techniques to prevent it.
Report this page